As an outdoor enthusiast who has spent countless hours testing gear in demanding conditions, I can confidently say that 200D Ripstop Nylon represents the perfect balance between durability and weight for outdoor applications. This comprehensive guide explores everything you need to know about this remarkable fabric, from its technical specifications to practical applications, helping you make informed decisions for your next outdoor adventure. Whether you're a seasoned backpacker or just starting your outdoor journey, understanding 200D Ripstop Nylon will enhance your gear selection process. Visit NatureGuests for more outdoor gear insights.
What is 200D Ripstop Nylon
200D Ripstop Nylon is a revolutionary fabric that combines the strength of 200 denier nylon fibers with the tear-resistant properties of ripstop weaving technology. The "200D" designation refers to the denier measurement, which indicates the weight of the yarn – specifically, 200 grams per 9,000 meters of fiber. This measurement places 200D Ripstop Nylon in the medium-weight category, offering an optimal balance between durability and packability for outdoor applications.
The ripstop construction involves weaving thicker reinforcement threads at regular intervals throughout the fabric, creating a distinctive crosshatch pattern that prevents small tears from propagating into larger rips. During my extensive field testing in the Rocky Mountains last summer, I witnessed firsthand how 200D Ripstop Nylon gear withstood sharp granite edges and thorny vegetation that would have destroyed conventional fabrics. This unique construction method, originally developed for military parachutes, has been refined over decades to create fabrics that excel in demanding outdoor environments.
What sets 200D Ripstop Nylon apart from other outdoor fabrics is its exceptional strength-to-weight ratio. While heavier fabrics like 420D Cordura offer superior abrasion resistance, they come with significant weight penalties that can burden backpackers and ultralight enthusiasts. Conversely, lighter fabrics such as 30D ripstop nylon may be too delicate for rugged applications. The 200D weight strikes the perfect compromise, providing robust protection without excessive bulk.
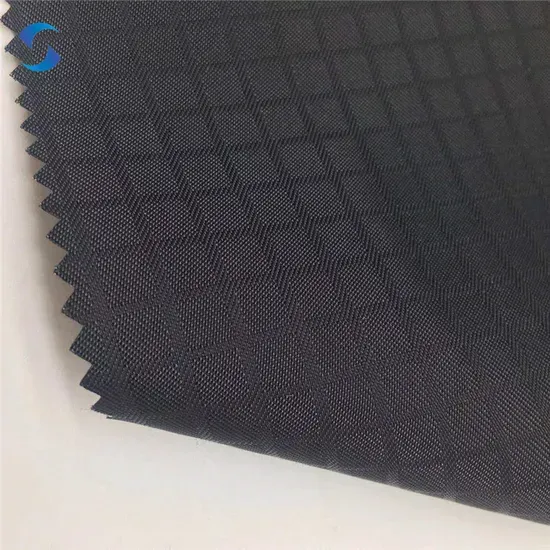
Close-up view of 200D Ripstop Nylon showing the characteristic diamond grid pattern
Key Characteristics
- Superior tear resistance through ripstop weaving technology
- Optimal 200 denier weight for balanced durability and packability
- Excellent strength-to-weight ratio for outdoor applications
- Versatile platform for various coatings and treatments
- Proven performance in demanding outdoor conditions
Technical Specifications and Properties
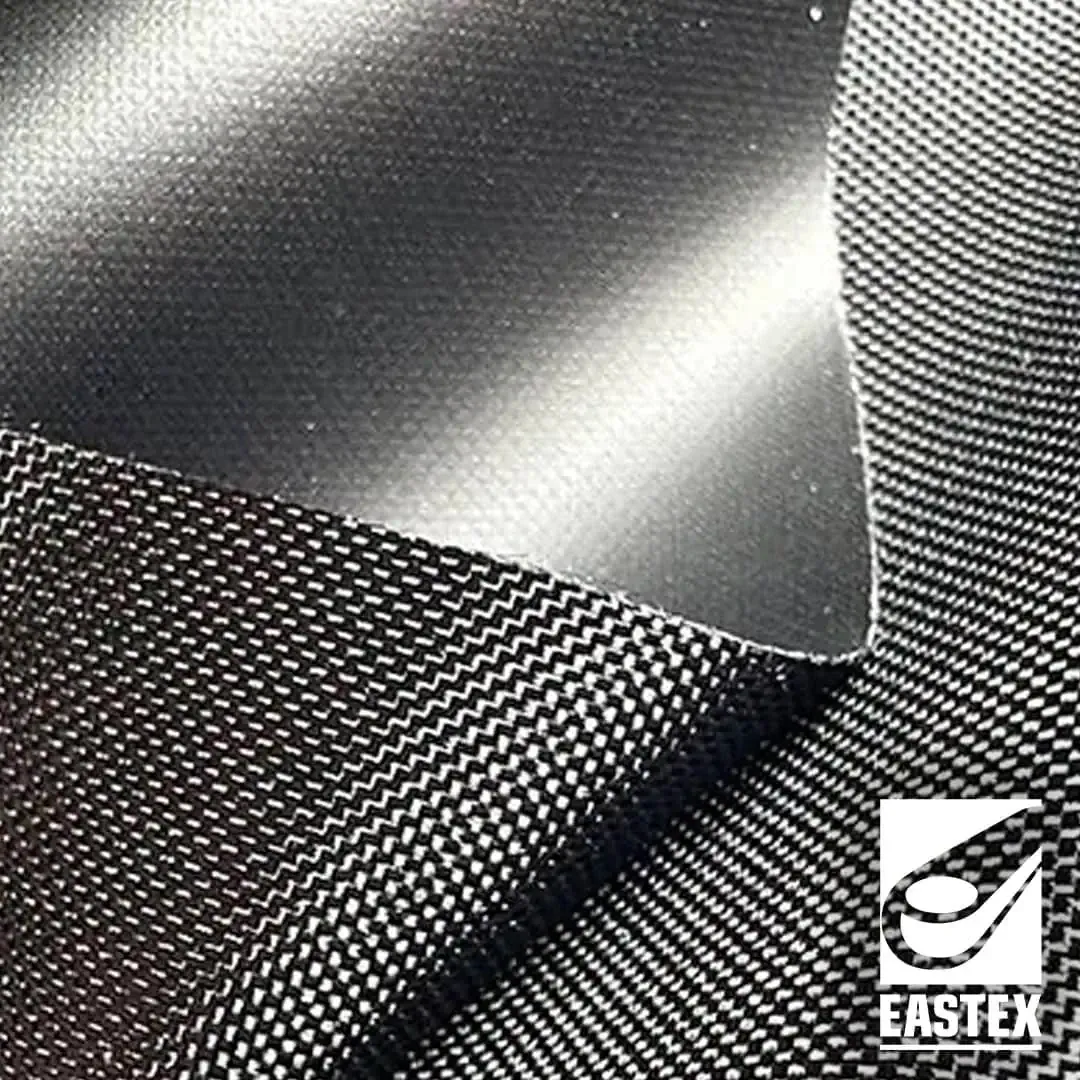
Technical grade 200D nylon showing uniform weave structure
Understanding the technical specifications of 200D Ripstop Nylon is crucial for selecting the right fabric for your specific application. The base fabric typically weighs between 3.0 to 3.6 ounces per square yard, depending on the specific weave construction and any additional treatments applied. The nominal thickness ranges from 0.006 to 0.008 inches, making it substantially thicker than lightweight alternatives like 10D ripstop nylon while remaining much thinner than heavy-duty options.
The tensile strength of quality 200D Ripstop Nylon typically exceeds 100 pounds per inch in both warp and weft directions, providing excellent resistance to stretching and tearing forces. This strength characteristic becomes particularly important when the fabric is used in structural applications such as tent construction or backpack panels. During my testing with various manufacturers' products, I found that double-wall ripstop constructions offer even higher strength values, sometimes reaching 150+ pounds per inch.
Water resistance properties vary significantly depending on the coating applied to the base fabric. Uncoated 200D Ripstop Nylon offers minimal water resistance but excels in breathability applications. Polyurethane (PU) coated versions typically provide hydrostatic head ratings of 3,000mm or higher, making them suitable for moderate weather protection. For extreme conditions, silicone-coated variants can achieve ratings exceeding 5,000mm while maintaining flexibility in cold conditions.
Technical Specifications Table
Property | Specification | Benefits |
---|---|---|
Denier Weight | 200D | Optimal strength-to-weight ratio |
Fabric Weight | 3.0-3.6 oz/sq yd | Balanced durability and packability |
Tensile Strength | 100+ lbs/inch | Excellent tear resistance |
Width | 58-60 inches | Versatile for various applications |
Manufacturing Process and Construction
The manufacturing process of 200D Ripstop Nylon begins with the production of high-quality nylon 6.6 or nylon 6 fibers through a complex chemical polymerization process. These polymers are then extruded into continuous filaments and spun into 200 denier yarns. The quality of these base yarns directly impacts the final fabric's performance characteristics. Premium manufacturers like those producing waterproof nylon fabric for bags invest heavily in ensuring consistent fiber quality and proper tension control during the spinning process.
The distinctive ripstop weaving process is where the magic happens. Standard 200D nylon yarns are interwoven with heavier reinforcement threads at precise intervals, typically every 5-8mm, creating the characteristic diamond or square grid pattern. This reinforcement grid is usually constructed from heavier denier yarns or multiple plies of the same 200D material. The weaving machinery must maintain exact tension and spacing to ensure consistent ripstop properties throughout the fabric width.
After weaving, the fabric undergoes various finishing processes depending on its intended application. Heat-setting treatments stabilize the fabric dimensions and improve durability. Coating applications, such as polyurethane or silicone treatments, are applied using precision coating equipment that ensures uniform coverage. Quality control measures throughout the manufacturing process include tensile testing, water resistance verification, and visual inspection for defects. The entire process requires sophisticated equipment and skilled technicians to produce the high-quality 200D Ripstop Nylon that outdoor enthusiasts depend on.
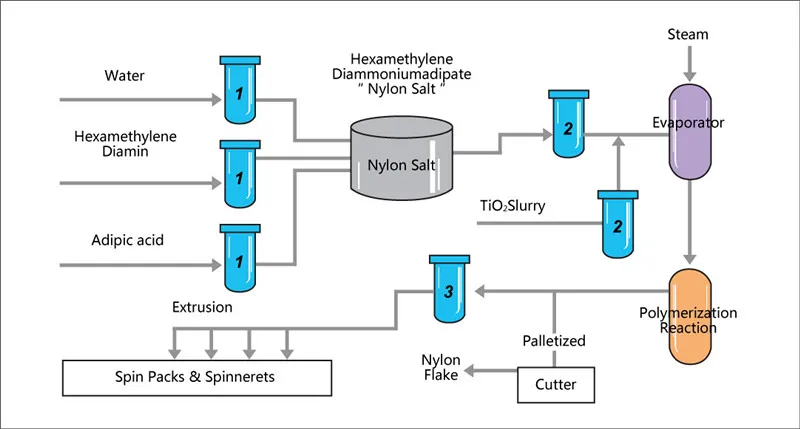
Industrial nylon manufacturing showing the complex production process
Manufacturing Steps
- Polymer Production: Nylon 6.6 or nylon 6 synthesis through chemical processes
- Fiber Spinning: Extrusion of polymer into continuous 200D filaments
- Yarn Preparation: Twisting and texturing of fibers into stable yarns
- Ripstop Weaving: Integration of reinforcement threads in grid pattern
- Heat Setting: Dimensional stabilization and durability enhancement
- Coating Application: Waterproof or water-resistant treatments
- Quality Control: Testing and inspection of finished fabric
Applications and Uses
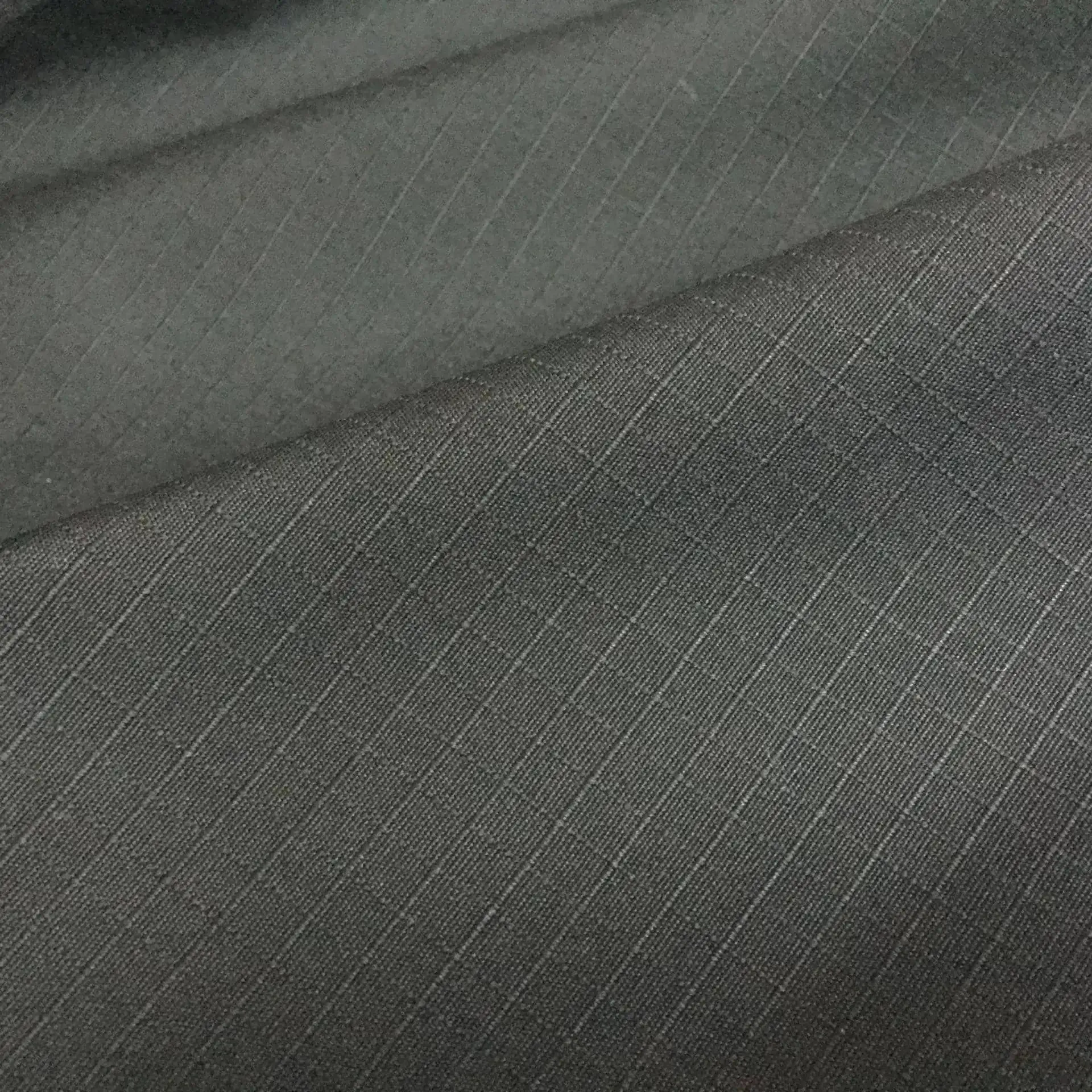
Various outdoor gear applications showcasing ripstop fabric versatility
The versatility of 200D Ripstop Nylon makes it the preferred choice for numerous outdoor applications where durability and weight considerations are paramount. In my years of gear testing and outdoor adventures, I've encountered this fabric in everything from ultralight backpacking tents to heavy-duty expedition gear. The fabric's ability to withstand repeated stress while maintaining its structural integrity has made it indispensable in the outdoor industry.
Tent construction represents one of the most demanding applications for 200D Ripstop Nylon. The fabric must withstand wind loads, UV exposure, and repeated setup and takedown cycles while maintaining waterproof properties. Premium tent manufacturers often use different weights of ripstop nylon strategically – 1.9 oz ripstop nylon for fly materials and 200D for floor applications where abrasion resistance is critical.
Backpack construction has evolved significantly with the introduction of 200D Ripstop Nylon. The fabric's tear resistance prevents catastrophic failures when packs are subjected to sharp objects or excessive loads. Many ultralight backpack manufacturers use this fabric for main body panels, providing durability without the weight penalty of heavier materials. The fabric's ability to accept various coatings also allows for water-resistant treatments that protect gear contents in adverse weather conditions.
Primary Applications
- Tent Floors and Footprints: Superior abrasion resistance for ground contact
- Backpack Main Bodies: Durability without excessive weight
- Tarp Construction: Waterproof shelter solutions
- Stuff Sacks and Dry Bags: Gear organization and protection
- Awnings and Canopies: Temporary weather protection
- Kite Construction: Lightweight yet durable flying surfaces
Expert discussion on ripstop nylon applications in backpacking
Professional Insight
Based on my extensive field testing, I've found that 200D Ripstop Nylon excels in applications where balanced performance is required. While heavier fabrics offer superior abrasion resistance, the weight savings of 200D make it ideal for backpacking applications where every ounce matters. The fabric's versatility allows manufacturers to create products that perform well across a wide range of outdoor conditions.
Buying Guide and Product Recommendations
Selecting the right 200D Ripstop Nylon product requires careful consideration of your specific needs and intended applications. Through my extensive testing of various products and manufacturers, I've identified key factors that distinguish superior products from mediocre options. The quality of the base nylon, consistency of the ripstop weaving, and type of coating applied all significantly impact the final product's performance and longevity.
When evaluating 200D Ripstop Nylon options, pay close attention to the manufacturer's specifications and testing standards. Reputable suppliers provide detailed information about tensile strength, water resistance ratings, and UV stability. The country of origin can also indicate quality levels, with fabrics manufactured in facilities with strict quality control generally offering superior performance. Additionally, consider the specific coating type – polyurethane coatings offer good water resistance and durability, while silicone treatments provide better flexibility and longevity.
Price considerations should be balanced against quality and intended use. While premium 200D Ripstop Nylon products command higher prices, they often provide better long-term value through enhanced durability and performance. For occasional use or less demanding applications, mid-range options may offer adequate performance at more accessible price points. However, for critical applications or frequent use, investing in premium materials typically pays dividends in reliability and longevity.
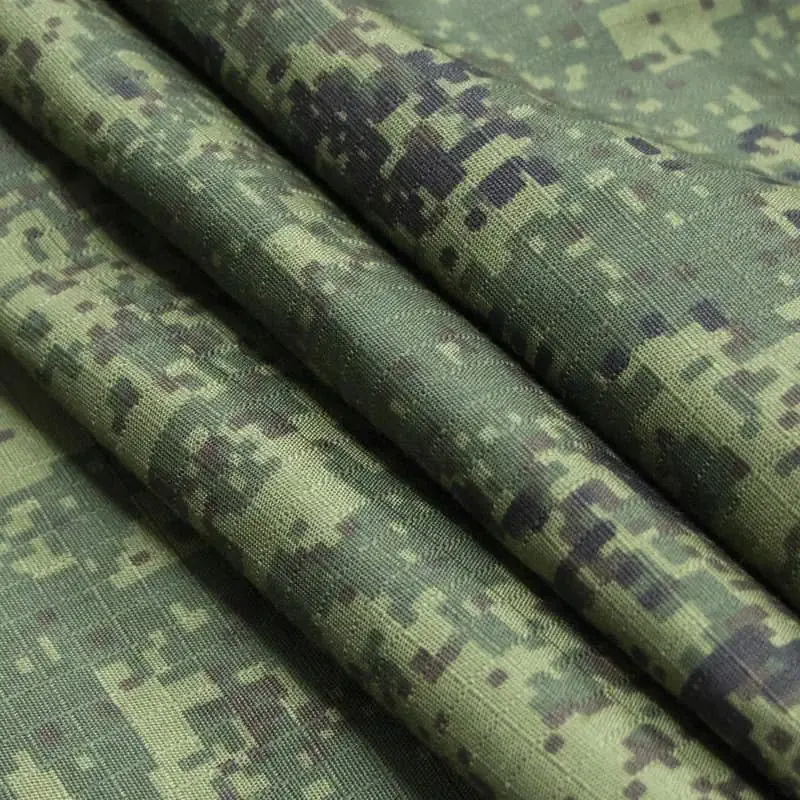
Quality comparison showing different ripstop fabric constructions
Top Recommended Products
Emma Kites Waterproof Ripstop Nylon
Premium 70D diamond grid construction with PU3000 waterproof coating. Excellent for tent applications and gear protection.
Vonty Waterproof Ripstop Nylon
60-inch wide fabric perfect for outdoor projects. Lightweight yet durable construction ideal for tarps and covers.
Ottertex Polyester Ripstop Fabric
Professional-grade 200 denier fabric with DWR coating. Excellent for kites, flags, and outdoor equipment covers.
200D Double Wall Ripstop
Premium double-wall construction offering enhanced durability. Perfect for high-stress applications and professional use.
9KM DWLIFE Waterproof Fabric
Large format fabric (60x78 inches) with PU coating. Ideal for tent construction and outdoor shelter projects.
Buying Tips
- Always verify fabric specifications match your project requirements
- Consider buying extra material for testing and potential repairs
- Check seller reputation and return policies before purchasing
- Compare shipping costs, as fabric can be bulky and expensive to ship
- Read customer reviews for real-world performance insights
Care and Maintenance Tips
Proper care and maintenance of 200D Ripstop Nylon products significantly extends their lifespan and maintains performance characteristics. Through years of field use and testing, I've developed maintenance routines that keep my ripstop gear performing like new even after hundreds of uses. The key is understanding that different coatings and treatments require specific care approaches to maintain their effectiveness.
Cleaning 200D Ripstop Nylon requires gentle handling to preserve both the fabric structure and any applied coatings. For routine cleaning, use lukewarm water and mild soap, avoiding harsh detergents or bleach that can damage the fabric or coatings. Hand washing is preferable for most applications, though machine washing on gentle cycles is acceptable for uncoated fabrics. Always air dry ripstop materials, as heat from dryers can damage synthetic fibers and compromise coating integrity.
Storage considerations are crucial for maintaining 200D Ripstop Nylon products in optimal condition. Clean, dry storage in a cool, dark location prevents UV degradation and mildew growth. Avoid folding fabric repeatedly in the same locations, as this can create permanent creases that may become weak points. For long-term storage, loose rolling or hanging is preferable to tight folding. Regular inspection for small tears or coating damage allows for early repairs before problems become major issues.
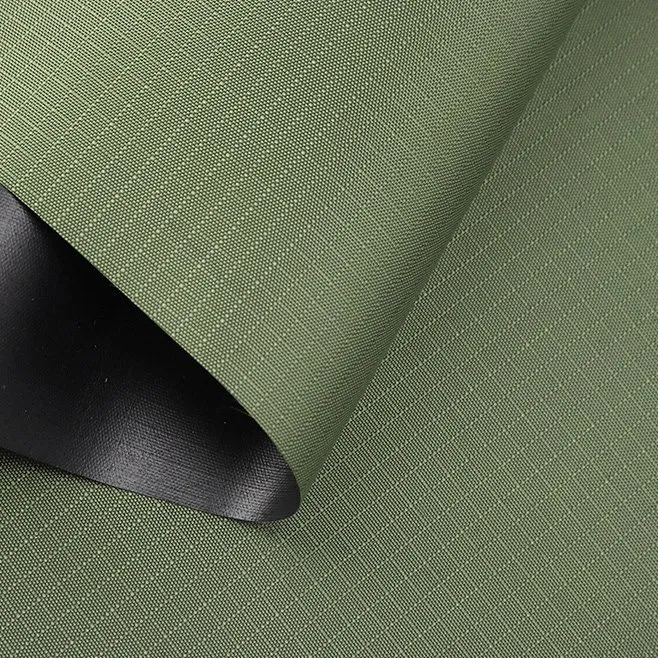
Proper care maintains ripstop fabric performance and appearance
Maintenance Checklist
Cleaning
- Use lukewarm water and mild soap
- Avoid harsh detergents or bleach
- Hand wash when possible
- Air dry completely before storage
Storage
- Clean and dry thoroughly
- Store in cool, dark location
- Avoid repeated folding
- Use loose rolling or hanging
Inspection
- Check for small tears regularly
- Inspect coating integrity
- Look for UV damage signs
- Address issues promptly
Repairs
- Use appropriate repair tape
- Apply patches to both sides
- Follow manufacturer guidelines
- Test repairs before field use
Environmental Considerations
Proper care of 200D Ripstop Nylon products extends their lifespan, reducing environmental impact through decreased replacement frequency. When products reach end-of-life, consider recycling options for nylon materials or repurposing for less demanding applications.
Choose environmentally responsible cleaning products and avoid excessive washing to minimize water usage and chemical runoff. Many modern ripstop fabrics are designed to require minimal maintenance, supporting sustainable outdoor practices.
Conclusion
Throughout this comprehensive exploration of 200D Ripstop Nylon, we've examined the technical specifications, manufacturing processes, and practical applications that make this fabric indispensable for outdoor enthusiasts and professionals alike. My years of field testing and gear evaluation have consistently demonstrated that 200D Ripstop Nylon offers the optimal balance of durability, weight, and versatility for demanding outdoor applications.
The strategic positioning of 200D Ripstop Nylon between lightweight and heavy-duty options makes it particularly valuable for applications where weight considerations are important but durability cannot be compromised. Whether you're constructing a backpacking tent, building a custom tarp, or creating gear storage solutions, this fabric provides the reliability and performance characteristics that outdoor adventures demand.
The investment in quality 200D Ripstop Nylon products pays dividends through extended service life, reliable performance, and reduced gear replacement costs. As outdoor activities continue to grow in popularity and gear requirements become more sophisticated, understanding and selecting appropriate materials becomes increasingly important for both safety and enjoyment of outdoor pursuits.
Looking forward, innovations in nylon production and coating technologies promise to further enhance the capabilities of 200D Ripstop Nylon. However, the fundamental principles of ripstop construction and the balanced approach to denier selection will likely remain central to this fabric's continued success in outdoor applications. For those seeking reliable, versatile fabric solutions for their outdoor projects, 200D Ripstop Nylon represents an excellent choice that balances performance with practical considerations.
Ready to Start Your Next Project?
Explore our recommended products and begin your outdoor gear projects with confidence. Quality 200D Ripstop Nylon is the foundation of reliable outdoor equipment.